Amber is a wholly-organic material derived from the resin of extinct species of
trees. In the dense forests of the Middle Cretaceous and Tertiary periods,
between 10 and 100 million years ago, these resin-bearing trees fell and were
carried by rivers to coastal regions. There, the trees and their resins became
covered with sediment, and over millions of years the resin hardened into amber.
Although many amber deposits remain in ocean residue, geological events often
repositioned the amber elsewhere.
For thousands of years, amber has been carved and worked into beads, jewelry,
and other types of ornamentation. However, today amber is valued primarily for
the astounding array of fossils preserved inside. As sticky resin was exuded by
the trees, animals, minerals, and plant materials were trapped in it. As the
resin hardened, these fossils-called inclusions-were perfectly preserved,
providing modern scientists with invaluable information about extinct
species.
Resin - Resin is a solid form of terpines obtained from pines and some other plants, mostly conifers, produced by heating fresh
liquid resin to vapourise the volatile liquid terpene components. It is semi-transparent
and varies in color from yellow to black. At room temperature it is brittle, but
it melts at stove-top temperatures. It chiefly consists of different resin
acids, especially abietic acid.
In industry it is the
precursor to the flux used in
soldering. The tin-lead solder commonly used in electronics has
about 1% Resin as a flux core helping the molten metal flow and making a better
connection. Resin is an ingredient in printing inks, varnishes, glues, medicines, chewing gum, soap, paper sizing, and, in the olden days, sealing wax.
It is
also extensively used for its friction-increasing capacity:
- Resining the bows of stringed
instruments such as violins or cellos to enhance sound production.
- Powdered Resin to keep gymnasts, weight lifters, and baseball pitchers hands dry and to increase their grip.
- Ballet slippers are also
rubbed in powdered Resin to reduce slipping.
- Pitch and Resin is mixed to to make a surface
against which glass is polished when making
optical instruments such as lenses.
- Painting - Resins
are added to painting media primarily for three reasons.
- First, a mixture
of drying oil and resin will offer a paint film that can be worked over
within hours or, at maximum, the next day because when the solvent
evaporates, which happens within several hours, the resin hardens, holding
the drying oil in place until it can oxidize and solidify.
- Second, a resin
may be used to dilute a paint for glazing without over thinning it. If a
glaze is too watery, it will run uncontrollably over the painting surface.
- Third, resins dry with greater clarity than drying oils and they will
add brilliance to paint films.
Types of Resins color> and Uses: color> color>
- Alkyd
Resin - color>Alkyd
resin is the category of resins that are made from mixtures of dibasic
acids and polyhydric alcohols. There are many alkyd resins and each
manufacturer picks a favorite and keeps it a secret. The quality and
concentration of an alkyd resin or medium can vary a great deal from
manufacturer to manufacturer. The selected resin is chemically combined
with a non-yellowing oil, such as safflower oil, producing a workable,
fast-drying medium. Most manufacturers add driers to speed up the drying
time and silica to give extra body. Alkyd
resins can exhibit a thixotropic effect. Thixotropy is an unusual
phenomenon where a gel or paste suddenly loses its plasticity when
disturbed or moved mechanically, resulting in a liquid. The opposite may
also occur where a liquid, left undisturbed, forms into a gel. This effect
can be used to advantage during glazing by helping to prevent the glaze
from spreading uncontrollably over the painted surface. However, this
characteristic is undesirable with impasto techniques. Alkyd resins should
not be over thinned, so add no more than 25 percent thinner to
resin.
- Colophony or colophonia resina - Resin is also known as
colophony or colophonia resina from its origin in Colophon, an ancient Ionic city. It is the resinous
constituent of the oleo-resin exuded by various species of pine, known in
commerce as crude turpentine. The separation of the
oleo-resin into the essential oil-spirit of turpentine and common Resin is
effected by distillation in large copper stills. Resin or colophony (Resin, U.S.P.) is the residue left after the removal, by
distillation, of the oil of turpentine from the crude oleoresin of Pinus
palustris, Mill., P. Taeda, Linn., and other species (N.O. Coniferae)
growing in Europe and the south-eastern United States.
- Copal - Copal
is a hard resin. Originally, the copal used in painting media was the
fossil resin amber. Now that amber is considered a semiprecious stone and
has become virtually unavailable to the artist, the copal available for
artists' use is unspecified tree-root resins. There are many grades
available on the world market and the best are rarely used for making
media. In addition to thickening a paint medium, adding leveling
properties to the paint film, and increasing gloss, this resin also
exhibits a thixotropic effect, which is particularly helpful in
glazing. Copal
is a hard resin which can only be liquefied through heating with a solvent
and so, when it dries, it is difficult to dissolve unless it is reheated.
This is a desirable characteristic because if a protective varnish such as
dammar has to be removed to clean or restore a painting, this can easily
be done without great risk of dissolving underlying paint films which
contain the copal resin. This insolubility at room temperature also means
that a copal varnish makes an excellent isolating varnish when applying
successive glazes. The
disadvantage of copal is that it darkens with age. Although the actual
reason for this darkening is not known, it is speculated that it is due to
changes that occur during the heating necessary to dissolve the resin.
Copal is brittle and is best used conservatively with a flexible drying
oil like stand oil. The difference between a "copal medium" and a "copal
varnish" is that the varnish often contains driers, which add to the risk
of cracking, and therefore the varnish is not best used in making a
painting medium. Today, many of the commercially made copal media have no
copal at all and are composed of synthetic substitutes or alkyd resins.
These substitutes are safer to use as a medium, being less brittle, but
they should not be used to replace copal varnish.
- Dammar - Dammar
is collected from the fir tree genus Shorea or from Hopea
trees of Southeast Asia. Dammar is a soft resin and is readily
dissolved in turpentine (not in mineral spirits, because it is then
partially insoluble) at room temperature and is the most popular additive
to a painting medium as well as the most commonly used resin for
varnishing. Dammar when used in painting media helps paint films to set up
quickly so that they may be worked over within a day. It is possible to
interlock paint layers by taking advantage of the two types of drying that
occur with a dammar-drying oil combination. Several hours after using this
combination, the dammar has hardened and the drying oil has begun to
polymerize through oxidation. If, in one and a half to two days, when the
drying oil is roughly half dry, a second paint layer containing the same
medium is applied, the two layers will interlock. The turpentine of the
medium when applied will redissolve part of the resin and soften the
drying oil of the paint film underneath, and the two should lock together.
This process can be used to produce beautiful and subtle effects. Dammar
also adds gloss and brilliance to a painting.
- Mastic - Mastic
is an exudate from the Mediterranean mastic shrub Pistazia lentiscus, also
known as the pistachia tree. Like dammar, it is a soft resin totally
soluble in turpentine and only partially soluble in mineral spirits. The
use of mastic resin in painting dates back to the time of Rembrandt and
the Dutch Masters and is responsible for Rembrandt's blue backgrounds now
appearing green. This is due to the yellowing of the mastic he used in the
application of five or six coats of varnish. Mastic is still popular today
primarily as an ingredient for media rather than as a varnish. The
yellowing effect of mastic is less pronounced when it is used in a medium
and many painters feel its advantages outweigh this drawback. One of the
advantages is that a mastic solution dries faster than all the resin
solutions-one hour in its pure form. It also dries clearer and with more
gloss than dammar. Many people who use mastic use it in combination with
dammar, fifty/fifty in a recipe calling for one or the other. This
ratio reduces the yellowing of the mastic and helps to speed the drying of
the dammar.
- Venice
Turpentine - Venice turpentine is collected in South Tyrol by boring the trunk of the larch
and collecting the oleoresin that slowly fills the cavity. It is a yellowish,
turbid oleoresin, consisting chiefly of a- and b-larinolic acid (55 to 60 per cent.), volatile oil
(20 per cent.), and resene (14 per cent.). A mixture of turpentine and resin is
often substituted for Venice turpentine (see Terebinthina Veneta Factitia). It is a viscous liquid resin; such resins
exude from certain trees and are often referred to as balsams. Venice
turpentine has been used in painting for centuries and has excellent
handling and aging characteristics. It should not be confused with the
thinners gum turpentine or rectified turpentine. Venice turpentine is used
as an additive to thicken other media. This resin is popular because it
gives body to the paint film while maintaining gloss and brilliance, and
it yellows very little over time. Genuine Venice turpentine is not easily found
and some companies are using a substitute resin called Canada balsam.
Canada balsam has two advantages over Venice turpentine-it dries more
clearly and it takes only one or two hours to dry, as opposed to three
days for Venice turpentine. However, Canada balsam has a distinct
disadvantage in that it is more fluid than Venice turpentine.
Method of Collecting Resin color>
In the collection of the
oleoresin in America a cavity is cut in the base of the tree-trunk during the
winter, into which a small quantity of the secretion contained in the normal
secretion ducts is discharged. The injury thus inflicted on the tree induces the
abundant formation of abnormal oleoresin ducts in the new wood. In the following
spring a triangular incision is cut above the cavity, from which a much larger
discharge of the oleoresin contained in these abnormal ducts takes place.
Further hacking, carried on at intervals during the summer, results in further
formation of abnormal oleoresin ducts and discharge of the oleoresin, large
quantities of which are thus produced. The oleoresin is then distilled with
water, oil of turpentine passing over, and resin (colophony) remaining in the
still; the fused resin is poured while still hot through wire strainers into
barrels, where it solidifies. The oleoresin obtained at first yields about 80
per cent. of pale yellow (amber) resin; later products contain more resin but it
is darker in colour (black resin). color>
The essential oil is
carried off at a temperature of between 100° and 160° C, leaving fluid Resin,
which is run off through a tap at the bottom of the still, and purified by
passing through straining wadding. Resin varies in color, according to the age
of the tree from whence the turpentine is drawn and the amount of heat applied
in distillation, from an opaque almost pitchy black substance through grades of
brown and yellow to an almost perfectly transparent colorless glassy mass. The
commercial grades are numerous, ranging by letters from A, the darkest, to N,
extra pale, superior to which are W, window glass, and WW, water white
varieties, the latter having about three times the value of the common
qualities. color>
Qualties and Composition: color>
- Resin is a brittle and friable resin, with a faint piny odor; the
melting-point varies with different specimens, some being semi-fluid at the
temperature of boiling water, while others melt at 100° to 120° C. color>
- It is very
flammable, burning with a smoky flame, so care should be taken when melting it.
When melted to a thick fluid, it can be surprisingly ductile. It is soluble in
alcohol, ether, benzene and chloroform color>
- Long-continued application of heat
causes darkening in the colour of the resin, while if the water is not entirely
removed an opaque resin is obtained. color>
- Resin occurs in amber-coloured,
translucent, compact masses, with a brittle, glassy fracture. color>
- The odour and
taste are slightly terebinthinate. color>
- The composition of resin consists of three isomeric abietic acids (a, b, and g), together with a small
quantity (5 to 6 per cent.) of resene, traces of volatile oil, and a bitter
principle. The resin acids appear to undergo change (probably oxidation) when
exposed to the air, and become less soluble in petroleum spirit. color>
- It is easily fusible, and burns with a dense,
yellowish smoke, leaving no appreciable ash. color>
- Specific gravity, 1.070 to 1.080.
Acid number, 150 to 180, and practically identical with the saponification
number. color>
- For pharmaceutical use resin should be pale in colour, possess a high
acid number, and be almost entirely soluble in petroleum spirit. By destructive
distillation it yields "resin spirit" and "resin oil." Resin spirit has, when
rectified, a specific gravity about 0.864, and distils mainly between 160° and
200°. color>
Action and Uses: color>
- Resin consists mainly of abietic acid,
and combines with caustic alkalis to form salts (Resinates or
pinates) that are known as Resin soaps. color>
- Inferior varnishes, color>
- Sealing-wax
and various adhesives.
color>
- Shoemakers' wax, color>
- Flux for soldering metals, f color>
- Pitching lager beer casks, color>
- Resining the bows of musical instruments and
numerous minor purposes. In color>
- Pharmaceuticals it forms an ingredient in several
plasters and ointments. color>
- Emplastrum Resinae, is used as
an adhesive plaster in minor surgery for strapping wounds. Unguentum Resinae, is
applied as a stimulant to indolent ulcers, boils, etc. Resin was formerly given
internally in rheumatism, sometimes with guaiacum resin. It is partly absorbed,
and excreted by the urine, and during excretion excites the kidneys to diuresis.
Sometimes so much is excreted in the urine that nitric acid causes a precipitate
of the resin, simulating albumin; the precipitate is readily distinguished from
albumin in that it is soluble in alcohol. Dose.-3 to 6 decigrams (5 to 10 grains). color>
- Ceratum Resinae, U.S.P. color>-Resin CERATE.
- Resin 35; yellow beeswax, 15; lard, 50.
- Ceratum Resinae Compositum, U.S.P.-COMPOUND
Resin CERATE.
- Resin, 22.5; yellow wax, 22.5; prepared suet, 30; turpentine, 11.5,
linseed oil, 13.5
- Emplastrum Resinae, B.P.-RESIN PLASTER. Syn.-Adhesive Plaster.
- Resin, 10; lead plaster, 80; hard soap, 5. Melt separately, using as
little heat as possible, then mix. Resin plaster is used in minor surgery to
draw together the edges of wounds, to apply dressings and as a protective. For
these purposes a thin backing of calico is usually preferred. For greater
protection the plaster may be spread on chamois leather, and for strength and
support on brown holland or moleskin.
- Parogenum
Terebinthinae, B.P.C.-TURPENTINE PAROGEN. Syn.-Turpentine Vasoliment. 1 (factitious
turpentine) in 5.
- Terebinthina Veneta Factitia, B.P.C.-FACTITIOUS
VENICE TURPENTINE.
- Resin, 62.5; linseed oil, 22.5; oil of turpentine, 15. The properties of
this mixture resemble those of oil of turpentine, and the preparation is
sometimes given internally as a diuretic, in doses of 2 decigrams (3 grains).
It is, however, used chiefly in the arts, and in veterinary medicine,
- Unguentum Resinae, B.P.-RESIN OINTMENT. Syn.-Basilicon Ointment.
- Resin, in powder, 8, yellow beeswax, 8; olive oil, by weight, 8; lard, 6.
Melt the resin and beeswax together, add the lard and oil, strain and stir
until cold. Resin ointment is mildly stimulating; it is applied on lint to
indolent sores and ulcers.
- Unguentum Resinae Compositum, B.P.C.-COMPOUND
RESIN OINTMENT.
- Resin, 20; oil of eucalyptus, by weight, 15; hard paraffin, 10; soft
paraffin, 55.
Gel or Gel Candles
color>
Resin is used to mix with mineral oil to make gel. Preffered mineral oil for gel
embeds needs to have a flash point of at least 425+°F and a
viscosity of 200. Four cups of resin mixes with 1 gallon of
mineral oil or 1 lb. bag of resin will gel 2 gal. of
mineral oil to a density equal 15 lb. color>
Utensils Required for making Gel or Gel Candles: color>
- metal spoon with a long handle.
- kitchen scale that measures ounces and by weight.
- measuring cup.
-
Kettle or cooking pot that is electrical with a built in thermostat.
- Food grade mineral oil
- Resin (Variations in colors from clear, yellow, to red or
amber, dark, to translucent)
- Glass container
- Oil based
fragrance and color are optional
Method for making Gel or Gel Candles:
- Measure 4 fluid cups of mineral oil and add to 1 cup
resin.
- Mix in heated pot and let set at room temperature for 30 min. or
longer - keep stirred.
- Slowly heat mixture until it reaches
200 - 220 degrees F. - hold this temperature until the gel is clear like water. (The mix should be free flowing). (Note: Do not allow the gel to heat higher than
240 degrees F.; if the gel gets hotter than 240 degrees F. it is reaching possible
flash point and will scorch -
having a burnt odor.)
- Stir the mix often while it cooks -
the gel might smoke slightly during the process. (Do not be alarmed but do not allow
excessive smoke this tells you that the temperature is rising to high)
- Add oil based fragrance or color to the mixture just
before you are ready to pour. This mix will hold as much as 1 oz. fragrance per
lb. gel.
- You can achieve different effects by pouring at various
temperatures. If you like lots of bubbles let gel cool to 200 degrees
F - letting the pour churn up bubbles. Pouring at 240° into a pre-heated
container gives fewer to no bubbles.
- To embed objects wait 2 - 5
min. after the intitial pour. Drop the embeds into place. Use extreme caution
when working with hot gel.
Standard Temperatures to remember:
- Heat gel to 225°
- Add
fragrance and color - 200°-225°
- Pouring temperature - 185°-200°
Projects to Consider:
- Gel can be used for decorations. Simply add
embeds to the gel and pour into a clear or semi-clear container.
- Embedding
souvenirs. Some people embed souvenirs...such as their favorite motor sports car
into a gel base.
- Floral vase - Gel can be made to look like water in a vase to
enhance the appearence of dried or silk floral arrangements.
- Natural or
Paraffin Wax candle holder -. Pour gel into a large glass container along with
embeds if desired. Place a wide mouth glass container into the top of the gel.
The embeded glass container will hold votives or natural wax candles...avoiding
the soot associated with Gel Candles.
Regions of Resin Production color>
- The chief region of Resin production is the South
Atlantic and Eastern Gulf states of the United States. American Resin is
obtained from the turpentine of Longleaf Pine Pinus palustris
and Loblolly
Pine P. taeda.
- The main source of supply in Europe is the French district of Les Landes
in the departments of Gironde and Landes, where the Maritime Pine P. pinaster is
extensively cultivated.
- In the north of Europe resin is obtained from the Scots Pine P.
sylvestris, and throughout European countries local supplies are obtained
from other species of pine, with Aleppo Pine P. halepensis being
particularly important in the Mediterranean region.
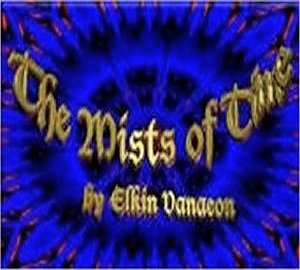
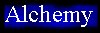
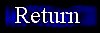

Idaho Web Design Tools